Fully Automatic Induction Heating Forging Production Line
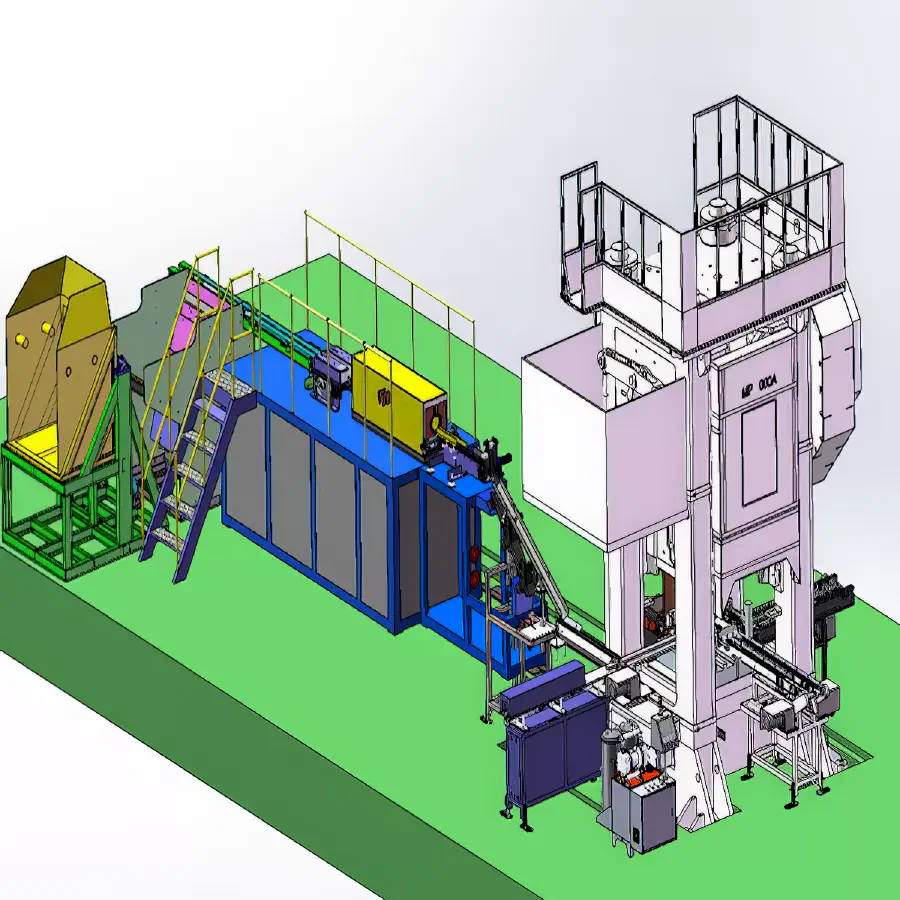
The fully automatic induction heating production line is a comprehensive production line that integrates induction heating technology, automation control, infrared temperature measurement technology and metal workpiece transmission. Its main purpose is to achieve efficient, uniform and continuous heating treatment of workpieces to meet the needs of various industrial productions.
Working principle of fully automatic induction heating production line:
First, the fully automatic induction heating production line converts alternating current into medium frequency induction alternating current through the power supply system. This medium frequency induction alternating current is then fed into the induction coil or work head via specially designed cables. When medium-frequency alternating current passes through the induction coil, it generates a high-frequency alternating magnetic field inside the coil.
Next, when the workpiece to be heated is placed in the induction coil, this medium-frequency alternating magnetic field will induce eddy currents inside the workpiece. These eddy currents are caused by the induced electromotive force generated by the movement of conductors in the workpiece in the magnetic field. The size and distribution of eddy currents depend on the shape, size, conductivity of the workpiece, and the strength and frequency of the magnetic field.
Due to the eddy currents generated inside the workpiece, according to Joule’s law, these eddy currents will generate heat when they flow inside the workpiece. The eddy current interacts with the resistance inside the workpiece to convert electrical energy into thermal energy, thereby heating the workpiece. This heating method directly heats the workpiece without conduction through external heat sources, so the heating speed is fast and the efficiency is high.
Through the above steps, the fully automatic induction heating production line completes the automatic heating of the workpiece.
Composition of fully automatic induction heating production line
Induction heating power supply: This is the core part of the fully automatic induction heating production line. It is responsible for converting electrical energy into medium-frequency alternating current to provide the required electrical energy for induction heating.
Induction heating furnace body: The induction heating furnace body of the fully automatic induction heating production line is the main place for heating the workpiece, and an induction coil is installed inside it. When the medium-frequency current passes through the induction coil of the Haishan electric furnace, a magnetic field is generated, which in turn generates eddy currents inside the workpiece to achieve heating. The furnace body design of Haishan electric furnace is usually customized according to the shape and size of the workpiece.
Automatic feeding and discharging system: This system is responsible for automatically feeding the workpieces to be heated into the Haishan electric furnace induction heating furnace body, and sending the workpieces out after the heating is completed. It ensures the continuity and efficiency of the production line.
Temperature control system: This system monitors the temperature of the workpiece in real time through a temperature sensor and adjusts the output power of the induction heating power supply according to the preset heating temperature to ensure uniformity and accuracy of heating. The fully automatic induction heating production line monitors and adjusts the heating process through precise control systems and sensors. The control system can automatically adjust the output power and frequency of the power supply according to the preset heating temperature, heating time, heating rate and other parameters to ensure that the workpiece can be heated to the required temperature evenly and quickly. The temperature control system automatically adjusts the output power of the induction heating equipment according to the preset heating temperature and heating time to ensure the consistency and stability of the heating effect. The safety protection system is responsible for monitoring the operating status of the entire production line, promptly discovering and handling possible abnormal situations, and ensuring the safe and stable operation of the production line.
PLC control system: PLC (programmable logic controller) is the “brain” of the entire production line. It is responsible for coordinating and controlling the work of each part of the fully automatic induction heating production line to ensure the stable operation of the production line. PLC can adjust the operating status of the production line according to preset programs or external signals. The automatic feeding system is responsible for automatically transporting the workpieces to be heated into the induction heating equipment and ensuring that the position of the workpieces is stable during the heating process. The fully automatic induction heating production line is also equipped with an automated feeding system and material transfer system to achieve automatic transportation and positioning of workpieces. These systems precisely control the position and movement speed of the workpiece through mechanical devices and sensors to ensure that the workpiece can be stably in the magnetic field of the induction coil during the heating process.
Cooling system: A large amount of heat will be generated during the induction heating process of the fully automatic induction heating production line. The cooling system of the Haishan electric furnace is responsible for dissipating the generated heat in time to prevent the equipment from overheating. This usually includes things like cooling water systems and cooling fans.
Safety protection system: including overheating protection, overcurrent protection, phase loss protection and other safety measures for the fully automatic induction heating production line, ensuring that the production line can automatically shut down under abnormal circumstances to avoid equipment damage and personal injury.
The fully automatic induction heating production line may also include other auxiliary equipment, such as transformers, capacitor banks, closed cooling towers, quenching spray pools, etc. These equipment together constitute a complete and efficient fully automatic induction heating production line.
Example of technical parameters of fully automatic induction heating production line
The total power of the fully automatic induction heating production line is about 1750kW (heating furnace 1350kW); the cycle time is less than or equal to 55 seconds per piece; the switching and debugging time is less than or equal to 20 minutes; workpiece material: 40Cr, 42CrMo; weight 5 ~ 40kg; workpiece rod length range: 800 ~1400mm; blanking length 0 ~1800mm; material diameter φ20 ~φ62mm; maximum heating length 600mm; floor space is approximately: 20m×10m (length×width).
Advantages of fully automatic induction heating production line
The advantage of a fully automatic induction heating production line is its high degree of automation and intelligence. Through precise control systems and advanced sensing technology, the production line can achieve precise control of the heating process and improve heating efficiency and quality. At the same time, automated feeding and material transfer systems can reduce manual intervention, reduce labor intensity, and improve production efficiency. In addition, the production line of Haishan Electric Furnace is highly flexible and scalable and can be customized and expanded according to different production needs.
In general, the fully automatic induction heating production line provides strong support for industrial production with its efficient, uniform, and continuous heating processing capabilities and high level of automation and intelligence. With the continuous advancement of science and technology and the continuous development of the industrial field, the application prospects of fully automatic induction heating production lines will be broader.